Kanban (jap. Karte, Zettel) ist ein System zur Planung und Steuerung des Materialflusses in der Produktion, es wurde vom japanischen Automobilproduzenten Toyota entwickelt. Das Kanban-System arbeitet nach dem Pull-Prinzip (Hol-Prinzip), woran sich bereits das Grundprinzip des Systems erschließen lässt. Die Produktion einer Fertigungsstufe wird ausschließlich durch den Verbrauch der nachgelagerten Fertigungsstufe ausgelöst, wenn diese die erforderliche Produktmenge selbständig anfordert bzw. abholt. Dabei wird ein Kanban-Signal, traditionell eine Kanban-Karte, weitergeleitet, welches die vorgelagerte Fertigungsstufe auffordert, mit der Produktion zu beginnen.
Die Zielsetzungen des Kanban-Systems sind die Reduzierung der Durchlaufzeiten, der Lagerbestände und des Steuerungsaufwands, wodurch Flächenbedarfe und Überproduktion abnehmen. Darüber hinaus können die Qualität und die Liefertreue gesteigert werden.
Das Kanban-System arbeitet nach dem Pull-Prinzip (Hol-Prinzip) und basiert im Wesentlichen auf einer dezentralen Steuerung des Materialflusses. Daraus resultiert, dass jedem Arbeiter im Kanban-System mehr Verantwortung zukommt, da dieser selbstständiger und eigenverantwortlicher arbeitet.
Der zuvor genannte Materialfluss ist in jedem Kanban-System vorwärts gerichtet, d.h. das Material durchläuft alle Produktionsschritte nur einmal und es ist keine Nachbearbeitung vorgesehen. Dem gegenüber gestellt ist ein Informationsfluss zwischen den einzelnen Produktionsschritten, welcher rückwärts gerichtet ist. Das heißt der Arbeiter des vorgelagerten Produktionsschrittes gibt mit Hilfe von Kanban-Signalen dem Arbeiter des nachgelagerten Produktionsschrittes Informationen darüber, wie viel dieser von welchen Vor- bzw. Zwischenprodukten benötigt. Diese Material- und Informationsflüsse wiederholen sich im Zuge der Produktion beliebig oft über alle Produktionsschritte.
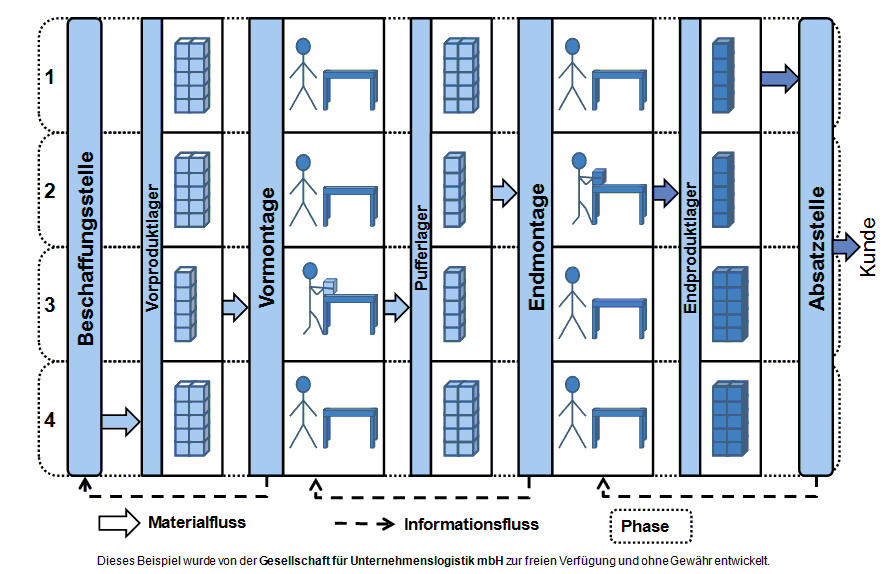
Bild 1: Arbeitsprinzip (Klicken um ein größeres Bild zu erhalten!)
(Eine genauere Erläuterung kann auf der Registerkarte "Links & Literatur" heruntergeladen werden.)